Technology is continuously advancing in the metal processing industry. Increased production needs and the demands of cutting metal of various shapes and thicknesses offer intense challenges to metal-cutting technology.
The competition in the metal processing industry has become fiercer, and with the continuous advancement of technology, CNC (Computer Numerical Control) laser cutting has gradually replaced traditional cutting methods. It has become a go-to choice in many industries.
This article will cover the main differences between CNC laser cutting and traditional cutting, helping you grasp a better understanding of how CNC laser cutting benefits compared to traditional methods.
What is a CNC cutter?
CNC cutting is a fabrication method that uses computer-controlled machines to produce complex designs on various materials. The term CNC stands for Computer Numerical Control. As the name implies, the machine's movements are directed by a computer using a numeric system.
A CNC cutter works by inputting a computer-aided design (CAD) into the system, and the process ensures that each piece is identical to the next, maintaining an impeccable standard of consistency.
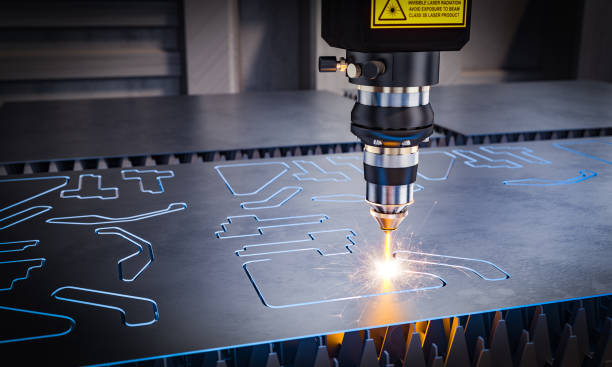
CNC Laser Cutting vs. Traditional Cutting: What’s the Difference?
Precision Difference
- CNC Laser Cutting
High Precision: CNC laser cutting ensures that each cut is flawless and results in micron-level accuracy. High precision enhances product quality while minimizing rework and reducing scrap rates.
Non-Contact Cutting: Mechanical stress can cause damage and deformation. The laser beam works without directly contacting the material, preventing damage and deformation.
- Traditional Cutting
Lower Precision: Traditional cutting methods such as shearing, stamping, and sawing are prone to errors, mainly when working with particularly complex shapes and parts.
Contact Cutting: Traditional cutting tools come directly in contact with the material, which can lead to deformation and damage.
Cost Effectiveness
- CNC Laser Cutting
Higher Initial Investment: CNC laser cutting machines involve a higher upfront investment. The need for tool replacements is rare, so repair and replacement costs are significantly reduced.
Low Maintenance Costs: Laser-cutting machines require low maintenance costs. So, the overall operating expenses are reduced. These machines also have a lengthier lifespan.
- Traditional Cutting
Lower Initial Investment: Traditional cutting equipment needs a lower initial investment, but its long-term operating costs are higher. Regular replacements and maintenance are necessary for the traditional cutting tools, increasing operational costs.
High Maintenance Costs: Traditional cutting equipment incurs higher maintenance costs. Operational expenses are increased with the requirement of regular inspections and tool replacements.
Production Efficiency
- CNC Laser Cutting
High Production Efficiency: CNC laser cutting guarantees high-speed and continuous cutting operations, improving production efficiency. It is flexible to handle various tasks for large-scale or small-batch production.
High Automation: Easy-to-operate and highly automated laser-cutting machines reduce the need for manual labor. It also increases the production efficiency.
- Traditional Cutting:
Slow Production Speed: The manual or semi-automatic operation in traditional cutting methods results in slower production speeds. It also affects the efficiency.
Labor-Intensive: In traditional cutting methods, skilled workers are required, hence increasing labor costs.
Application Range
- CNC Laser Cutting
Wide Applicability: CNC laser cutting technology is suitable for metal, plastics, wood, and composite materials. Offers creative freedom for designers by handling many intricate shapes and patterns.
High Flexibility: A CNClaser cutter for metal and other materials is affordable and adaptable to various applications, as it can easily manage various cutting tasks.
- Traditional Cutting:
Limited Applicability: Traditional cutting methods are only suitable for simple shapes and specific types of materials. It is hard to deal with complex shapes and special materials.
Low Flexibility: Traditional cutting methods have limited flexibility as they are less equipped to meet diverse cutting needs.
Environmental Impact
- CNC Laser Cutting:
Environmentally Friendly: The laser cutting process begets minimal waste and meets environmental standards. In CNC laser cutting, there is no emission of dust or harmful gas, hence contributing to a protected environment and employee health.
Low Energy Consumption: Lower energy consumption of laser cutting machines helps companies achieve emission reduction goals and saves energy.
- Traditional Cutting:
Environmental Pollution: In traditional cutting methods, a lot of harmful substances and waste are produced, harming the environment.
High Energy Consumption: Traditional cutting equipment takes up more energy, which is not conducive to sustainable development.
Conclusion
Unlike traditional cutting methods, CNC laser cutting technology offers higher precision, lower maintenance costs, higher production efficiency, a wider application range, and a positive impact on the environment. Adopting CNC laser cutting technology can help businesses thrive in competitive markets and attain sustainable development.